
The sequence of operations for the investment casting is determined on the basis of the layout of the investment casting line. Investment casting has been clearly identified as the process to use to form the initial billet. The cost of any casting increases in proportion to the preciseness of specifications, whether on chemistry, non-destructive testing or tolerance brands. One factor which however remains constant.

The amount of tolerance required to cover each process step is dependent, basically, on the size and shape of the casting and will vary from foundry to foundry.
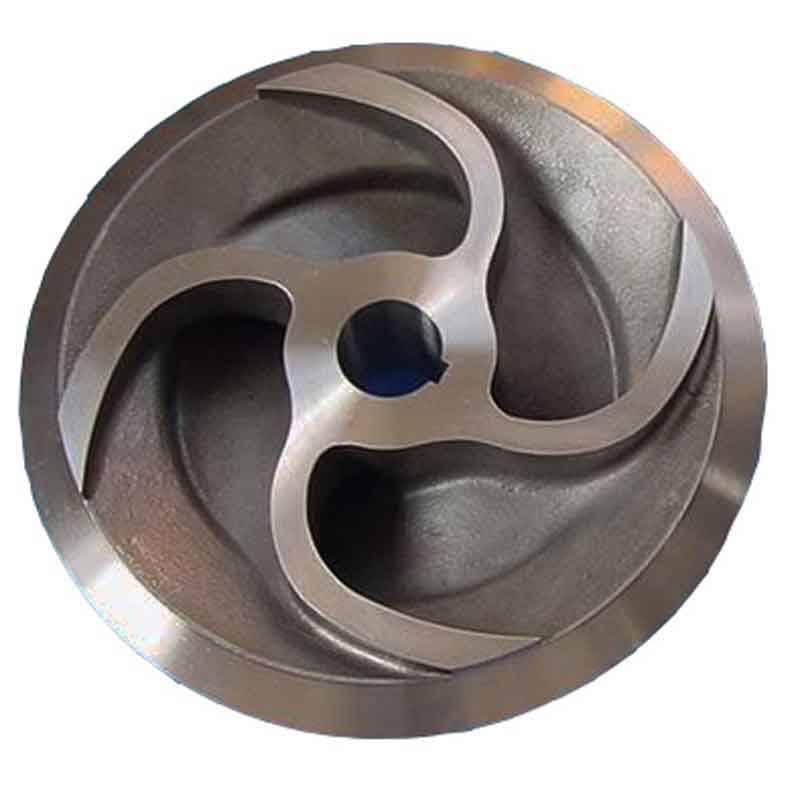
The design for investment casting include wax, or plastic temperature, heat treatment temperature all bear directly on tolerances required in the investment casting process. Metal is then poured into the remaining cavity. The model is then removed by using an autoclave or furnace. Investment Casting is a process of using a sacrificial pattern, which is coated with a ceramic shell. Iron casting foundry India uses different kinds of sand depending on the application and the nature of molding process. The stages involved in the sand molding process include sand preparation, pattern making, core making, molding, and closing. These are used for over seventy percent of castings produced. The casting process involving the use of sand as molding medium can be classified as a sand molding process. Calmet ensures that each casting is processed through our QC staff with inspection records for every shipment. Iron casting foundry India takes more care in the selection and production of suitable pattern equipment. This includes pre-casting, casting, post-casting. Iron casting foundry India follow three stages of the casting process. Calmet supplies ferrous and non – ferrous castings made at fully- automated / semi-automated foundries located across Asia. Iron casting foundry India is classified as Steel/Alloy/ Stainless Steel foundries, Grey Iron Foundries, Ductile Iron (SG Iron) Foundries, Non-Ferrous Foundries, Artware Foundries. In terms of a number of operating units, India ranks 2nd after China as far as a number of operating foundries are concerned. Metal casting has been an art long before it was a science. Iron casting foundry India has been the most sought after by companies in the USA and Europe. We are ready to offer customers the best service in diverse and flexible ways according to customers′ needs.A foundry is a factory that produces metal castings.

K., Denmark, Japan, Australia, Korea, and etc.Under the principle of equity and mutual benefits, we always abide by the concluded contracts and keep our promises. We has established good business relationships with the oversea customers from U. We will supply customers with excellent quality, reasonable price, punctual delivery, classification certificates and other quality certificates as required. We has experienced engineers and quality control people and can develop and design products separately or coordinated with customers according to customer′s request, to meet the requirements of different customers. Technical method: Sand cast, lost wax cast/investment casting, lost foam cast, gravity cast, die cast, low pressure cast, centrifugal cast, shell-core & mould cast. Gray iron castings/cast iron, Ductile iron castings/Spheroidal/Nodular Graphite castings,Īluminium castings, Steel castings, Brass and bronze castings Our company have been specializing in manufacturing and exporting all kinds of casting products, mainly as follows:Įxport of various castings and machined products
